H2 COPRA RF Analysis Tools
Deformation Technology Module
COPRA RF DTM is a fast and secure software module for pre-optimizing of the forming process. It determines the maximum occurring values of deformation in longitudinal direction. Therefore, it allows to quickly evaluate the feasibility of a project even without the optional FEA simulation.
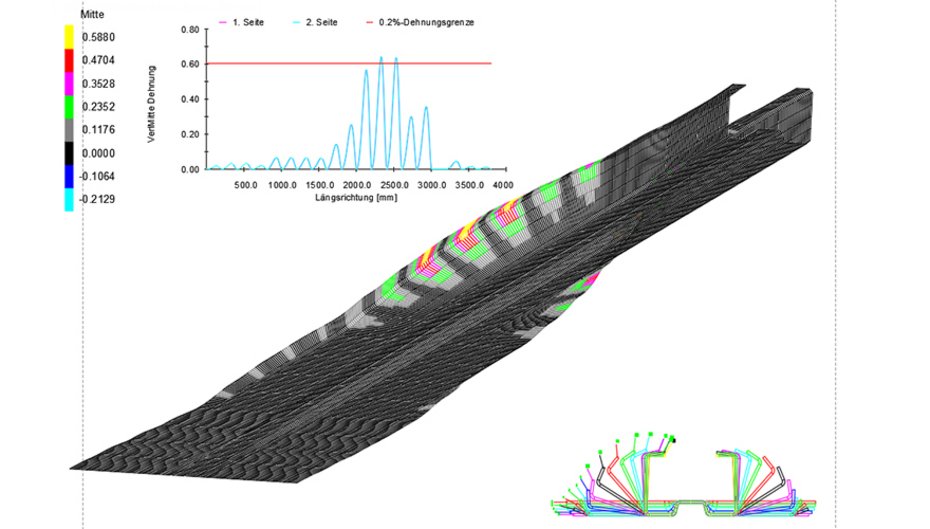
COPRA RF DTM - at a glance
- Calculation of deformation in longitudinal direction
- Pre-optimization of forming process
- Perfect extension to COPRA FEA RF
- Prevents profile deficiencies
During roll forming, unwanted plastic longitudinal elongation often occurs - mostly at the strip edges. The effects are various defects of the product such as twist, bow or end flare. COPRA RF DTM is a strictly geometrical program and calculates the strain forces reliably and quickly.
The generated model is based on the theory of thin shells. Due to the minimal computing time the roll set is pre-optimized quickly and reliably. COPRA RF DTM includes parameters like profile shape, or the length of the forming zones based on the roll diameter. Subsequently, the designer can conduct a more promising FEA-simulation.
For pre-optimization, the designer only needs to define the flower and provide a small amount of data. Until today COPRA RF DTM is the only software that can calculate strip elongations taking into account the roll diameter.