COPRA RLM – Intelligent Roll Management
Managing and storing large roll stocks is time-consuming and expensive for roll formers. Our tool database COPRA RLM makes efficient use even of large roll pools with the help of intelligent management functions - for accurately matching roll tools and the possibility of reuse.
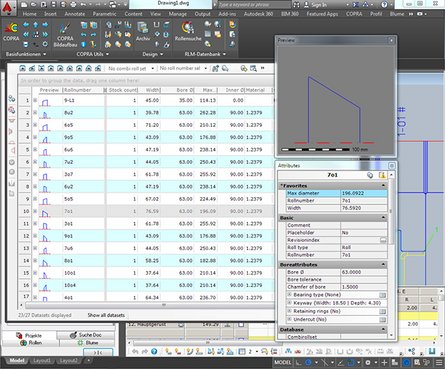
COPRA RLM - at a glance
- Quick and easy management even of large roll stocks, cost reduction through efficient use
- Advanced search feature with numerous parameters (bore diameter, roll width, etc.)
- Real-time search during the design process with SmartSearch
- Automatic compiling of order lists
- Quality control with COPRA RLM and COPRA RollScanner
- Complete integration with COPRA workflow
- Efficient reworking of worn rolls
COPRA RLM offers a variety of intelligent management functions and represents an integral part of the COPRA workflow. With Foundation, Professional and Ultimate, three individual modules with different ranges of functions are available.
RLM Foundation - Powerful Roll Database
Since many rolls are required for the manufacturing of new products, there are often delays due to the tedious search for the appropriate tools. With SmartSearch, however, an automated real-time search for the suitable roll tools can be carried out even during the design phase - all it takes is a simple click on a profile element.
The designer simply selects the suitable rolls from the visually displayed output. This also eliminates the necessity of defining roll attributes - the life cycle of a roll can thus be tracked in detail. The extended search function also allows rolls to be found on the basis of numerous parameters, such as roll width or bore diameter.
RLM Foundation offers a wide range of functions for searching the stock on the basis of definable criteria and thus finding the appropriate rolls quickly. The basis for this is the Microsoft SQL Server. Due to the integration within the COPRA workflow, the rolls are imported back to the design department and are available for further processing.
RLM Professional - booking in and out, order parts lists
In addition to the basic functionality, the COPRA RLM Professional module offers an integrated warehouse management and an ordering system. For a new project RLM automatically calculates order parts lists based on the current stock. When tool sets are changed frequently, employees can use simple handheld scanners to book the rolls out of inventory and release them for use, reworking or scrapping. In this way, inventory always remains up-to-date and only those rolls that are actually needed need to be ordered.
RLM Ultimate - efficient post-processing of rolls with Regrind
The COPRA RLM Ultimate package additionally offers customers the possibility of recycling roll tools. The Regrind function is a prime example of how hardware and software solutions can be utilized efficiently within the COPRA workflow. Thus, since the 2017 release, COPRA RF together with COPRA RLM as well as COPRA RollScanner offers a worldwide unique function for the reworking of roll tools without major effort. The software identifies rolls with the highest wear and calculates the values by which the rolls need to be reworked.
In this way, old rolls can also be reintegrated into the production process. Such stocks have often been sitting unused in the warehouse for years, although they could be reused by simply reworking them. This opportunity often remains unused despite the great potential for savings in the industry.
AssemblyCheck
Start-up of roll forming line without mishaps
Together with the standard module COPRA RF and the COPRA RollScanner, RLM provides the particularly practical AssemblyCheck function. It significantly facilitates the start-up of a roll forming line. The COPRA RollScanner measures the roll contours, which are subsequently processed and compared. Deviations appear immediately, and incorrect positions in the bending areas can thus be avoided in advance. After adjustments of individual roll tools, the entire design is automatically updated.