COPRA RollScanner more than just quality control
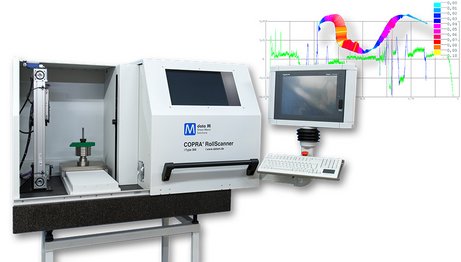
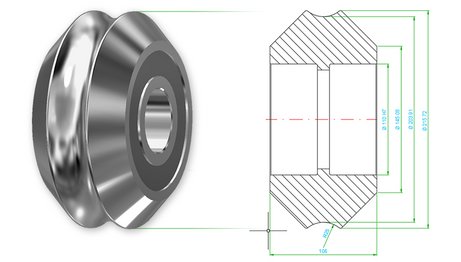
There is no doubt about the many advantages of CAD/CAM software for the layout of tube mill rolls or roll form tooling.
But does the actual geometry really meet the original design? Even a minor deviation from the original roll contour may result in falty tubes or profiles.
The COPRA RollScanner not only samples roll data but also allows for quality control and roll shape analysis – the first step in the optimization of your tooling.
Automatic Roll Inspection Machine for Quality Control, Reworking and Reverse Engineering
Highest Accuracy
…For your total quality approach
The COPRA RollScanner generates an accurate set of data of a roll's true shape. Scanned rolls can be compared immediately to the originally designed contour. This means no more "fire-fightings" due to unexpected and unnecessary long try-outs. Rolls can be reworked even before being put into operation.
Profit from used rolls
...Scanning complete roll sets
This device offers a new way of analyzing and optimizing existing roll sets without having any original drawing. The integrated vision system generates an accurate set of coordinates (also DXF files) of the contour.
With every roll transferred to the COPRA Database you will also be able to see the original forming sequence (flower pattern) on your monitor.
Reverse engineering allows the analysis of actual roll tooling
...get the original forming sequence
Extract reshaping concepts easily out of existing roll sets. The new set will be built from the scanned contours with COPRA RF, whereby the existing reshaping strategy can be traced back. The construction can be simulated and optimized thereafter.
Design and Simulation Service
...data M Engineering Center
Our engineering team looks back on many years of experience in roll design and tool engineering. We are happy to offer our design and optimization services to our customers. From the first design layout to scanning your roll sets with the COPRA RollScanner up to Finite Element Analysis we will accompany you as your competent partner.
COPRA Software Technology
…for optimum roll design
The design and simulation software COPRA RF has become the market leader in tube mill roll design and roll form engineering.
As one of the first software and engineering companies has data M Sheet Metal Solutions GmbH developed its own simulation software. The unique COPRA RF DTM (Deformation Technology Module) and COPRA FEA RF (Finite Element Analysis) offers you the possibility to optimize your design and your roll tooling already during the engineering process and enables you to establish a new quality standard for the entire production process.