COPRA FEA RF - The virtual roll forming line
Our simulation software COPRA FEA RF renders cost-intensive trial and error processes obsolete. The module calculates even complex roll forming operations with hundreds of stations as well as pre- and post-processing manufacturing steps reliably and fast. Model creation is fully automized - there is no need for a dedicated FEA specialist.
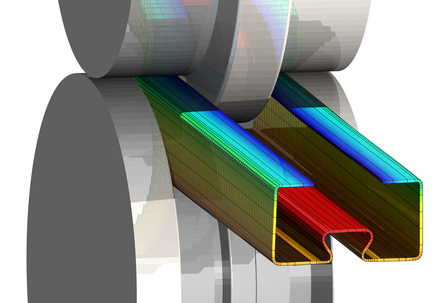
Analysis Software
COPRA FEA RF is used to simulate the roll forming operation by non-linear elastoplastic calculation.
In the past roll forming used to be treated as a "black art". Difficulties such as appearing faults and problems in setting up new roll sets on the mill were not uncommon. In a trial & error approach one had to produce a whole roll set and do the machine set-up in order to find potential weaknesses in the rollforming process - a costly and time-consuming approach causing undesired machine down-times.
What´s new in COPRA FEA RF 2025.1
With over 20 years of FEA simulation experience in research and industry our specialists have contributed to the COPRA FEA RF continuous improvement. This is a selection of new features available in the software:
- Efficient Post-Processing with User Defined Range Sets
- Improved User Experience in COPRA FEA RF Model Setup (COPRA2FEA)
- Advanced Possibilities to Define Position and Orientation of Cross Sections
- New Post-Processing Results in COPRA FEA RF Wirerolling: Distance to Tooling or Cross Section
- Marc/Mentat 2024.1 Included (also for COPRA FEA RF WireRolling)
data M has been aware of this problem from an early stage and has concentrated their efforts into developing a simulation program to overcome these problems. It is now possible to predict the practical results with high accuracy with COPRA RollForm Simulation Technology.
Non-linear Finite Element Analysis
With the COPRA FEA RF module data M continues to supply highly efficient software packages tailored to the roll forming industry´s needs. The program imports data directly from COPRA RF and it provides essential information about forces, torques, stresses, strains and a 3D-visualization of the final product showing possible later deformations. As a matter of fact, this module can be regarded as a "virtual roll forming mill" that allows the user to try out new roll sets even before the actual manufacturing process.
COPRA FEA RF can be operated easily and runs on any personal computer. It does not require any time-consuming pre-processing or difficult post-processings. It is tailored to the roll former´s needs - as are all of data M COPRA RF products.
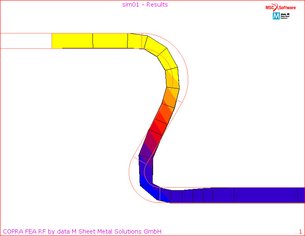
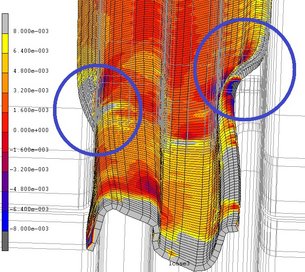
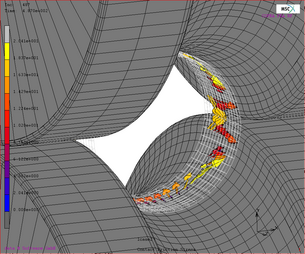