R&D, Design, Engineering and Software Services
For many years data M has been well known for its services. The combination of experience and competence with hardware and software tools makes data M a valuable partner for your activities in research, design and process optimization.
There are many reasons why companies turn to data M for assistance. The following keywords give a rough impression of scenarios:
- The project is not within the customer's core competence and may only need to be carried out once. Investment in software products and staff training would not pay off
- (Temporarily) insufficient design capacity.
- The customer needs additional resources and a competent partner for a research project or a special highlight for an exhibition.
- Limited time to market (need for a right first time solution)
- The customer needs a turnkey and competitive solution
- The customer needs support for increasing knowledge of the process and speed up progress.
- Reduction of wear, downtimes and energy consumption in high volume production processes
- The customer got stuck in a specific project / learning purpose
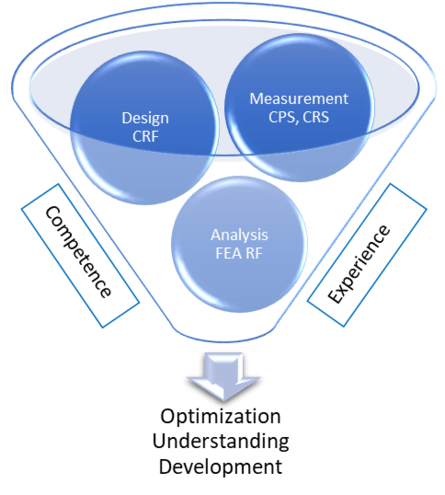
Approach:
- FEA based analysis
- Tool design
- Measuring data (roll tooling, profile quality)
- Competence and experience
- Optimization / Understanding / Development
Outcome:
- Analysis and optimization report
- Tool design documents
- Roll manufacturing
- Better understanding of process
- Process optimization
- Research and Development
Our Service Packages
- Design of a new tool set with COPRA RF (flower, strip width, FTM, rolls, etc)or representing a given design in COPRA RF, including verification and optimization with COPRA FEA RF
- Outcome (selectively)
- COPRA Archive
- DXF contours, NC turning program, DXF-contours, dimensioned roll drawings
- Assembly plans
- Understanding of profile geometry, remaining stresses and process stability.
- Analysis Report (illustrating the optimization steps and expected process and profile quality)
- Roll manufacturing at our approved roll manufacturer (with Rollscan report)
These could apply to a single purpose toolset but also a toolset for a specific range of product sizes. There is almost no limit to the profile type: construction profiles, automotive or aviation parts, high precision ball bearing telescopic slides, thin walled heat exchanger or medical tubes up to large diameter tubes for oil transport, trapezoidal sections, etc.
A good design cannot provide the absolute reliability of a well ran production, but may increase the stability and provide a better understanding of process sensitivity (e.g. with varying material, machine and environmental parameters).
- Representation of the design in COPRA RF
- Representation and investigation of the forming process in COPRA FEA RF
- Outcome (selective)
- Understanding of correlation between forming process and profile quality
- Identification of optimization potential
- Development and FEA based verification of optimization strategies
- Analysis Report (illustrating the initial profile and process quality as well as the expected influence of the developed optimization strategies)
Most of the process listed above are notably high precision, high volume or cost intensive (like cage mill setup) roll forming production processes.
Another purpose of this service can be to increase the stability of (e.g. high volume) production: reduction of maintenance times, wear of tooling and energy consumption will increase steady profits.
- Profile scanning with COPRA Profile Scan
- (optional) Verification of the forming process in COPRA FEA RF
- Outcome (selective):
- Profile drawing
- Profile measurement protocol
- Understanding of profile quality
- Understanding of correlation between forming process and profile geometry
- Preparation of models in COPRA RF and COPRA FEA RF to represent the pre-operation process
- Simulation and investigation of the pre-operation step
- Simulation of the subsequent roll forming process taking into account the results of the pre-operation step
- Outcome (selective):
- Analysis Report showing the outcome of the study (standard investigation representing the forming process and discussion of customer related questions)
- Modification / Optimization steps
Any operation on the flat sheet may be worth to investigate - from embossing and punching through the levelling and straightening process up to special heat treatments.
- Represantiation and simulation of the roll forming process in COPRA RF and FEA RF
- Preparation of models in COPRA RF and COPRA FEA RF to represent the post-operation process (e.g. tooling from CAD and/or kinematics)
- Simulation of the post operation with and without considering the preceding roll forming process
- Outcome (selective):
- Analysis Report showing the outcome of the study (standard investigation representing the forming process and discussion of customer related questions)
- Modification / Optimization steps
- Preliminary investigation of FEA capabilities
- Preparation and tests of representative FEA models
- Outcome (selective):
- Workshop with customer for know-how transfer
- Apply model in design / optimization steps
These apply to processes like HF welding with an electro-magneto-thermo-mechanical coupled representation of the process, or processes with complex kinematics like stretch bending, mandrel bending or roll forming winding processes to produce flex tubes.
- Similar to roll forming, this can mean either the optimization of an existing tool set or the design and layout of a tool set for new wire profiles.
- Feasibility studies of flexible roll formed parts (truck beams, aircraft structures, automotive parts)
- Optimization process
- Production of prototype parts
- Development and layout of tooling and machines for industrial application