H2 COPRA RF Analysis Tools
Formänderungstechnologie
COPRA RF DTM ist ein schnelles und sicheres Softwaremodul zur Vor-Optimierung des Umformprozesses. Es ermittelt die maximal auftretenden Werte der Formänderung in Längsrichtung. So lässt sich auch ohne die optionale FEA-Simulation schnell ermitteln, ob ein Projekt umsetzbar ist.
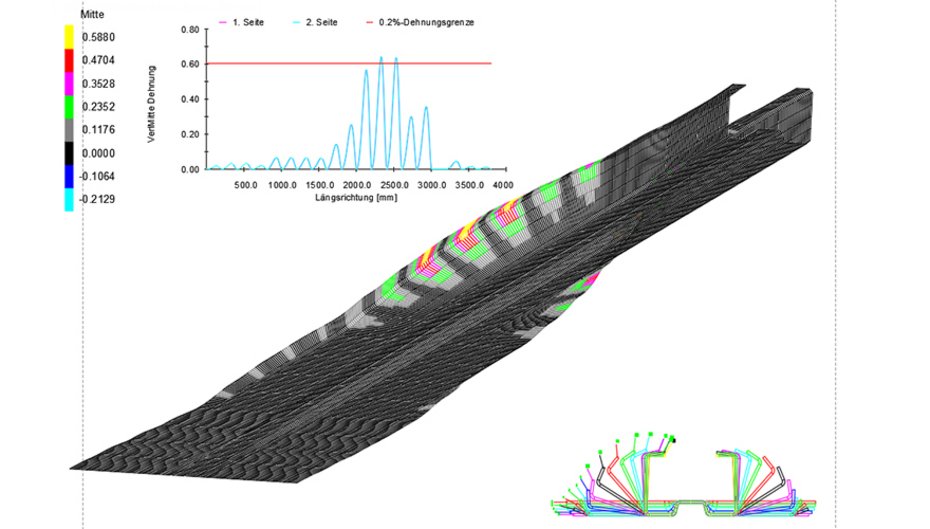
COPRA RF DTM - auf einen Blick
- Berechnung der Formänderung in Längsrichtung
- Vor-Optimierung der Umformung
- Ideale Ergänzung zu COPRA FEA RF
- Vermeidet Defekte am Profil
Beim Walzprofilieren kommt es nicht selten zu unerwünschten plastischen Längsdehnungen - meist an den Bandkanten. Die Folge sind unterschiedliche Defekte am Produkt wie z. B. Drall, Krümmung oder Kopfsprung. COPRA RF DTM ist ein rein geometrisches Programm und berechnet die Dehnungskräfte zuverlässig und schnell.
Das generierte Modell basiert dabei auf der Theorie der dünnen Schalen. Durch die minimale Rechenzeit wird der Rollensatz schnell und zuverlässig voroptimiert. COPRA RF DTM berücksichtigt dabei Parameter wie die Profilform oder die Länge der Einformzonen, basierend auf dem Rollendurchmesser. Anschließend kann der Konstrukteur noch eine FEA-Simulation erfolgversprechend durchführen.
Für die Vor-Optimierung muss der Konstrukteur lediglich die Profilblume definieren sowie wenige Daten eingeben. Bis heute ist COPRA RF DTM die einzige Software, die Banddehnungen unter Berücksichtigung des Rollendurchmessers berechnen kann.