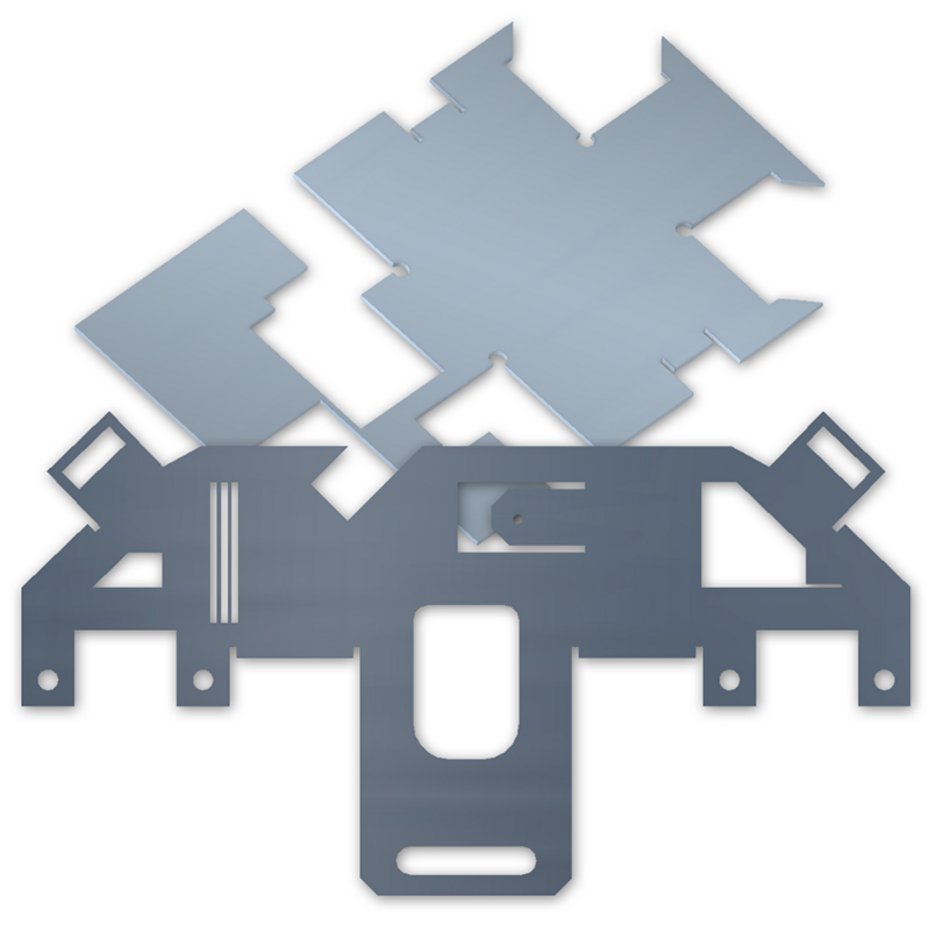
COPRA MetalBender Solver
Top solution for flat pattern calculation of all kinds of sheet metal parts
Flat pattern calculation for everybody. COPRA MetalBender Solver is a tool easy to use for anybody who designs and manufactures sheet metal bending parts with AutoCAD Mechanical or AutoCAD.
The COPRA MetalBender Solver is perfectly integrated in the user environment of AutoCAD Mechanical and calculates the exact flat pattern geometry of 3D sheet metal parts including overbending angle and -radii. The flat pattern can be calculated for the neutral line as a membrane model or for the inner and outer side taking into account the different intersection curves of break-through objects intersecting the sheet metal part in a non-perpendicular angle. The optional reduction of the intersection points or automatic conversion into arcs allows an optimised production sequence. For the calculation of the neutral line the methods according to DIN 6935, material properties, machine correction tables or experience values are available. The overbend angle and -radii are calculated taking the material properties and bending method into account.
The flat pattern is calculated within seconds. It includes the correct unbended dimensions with bend lines, bend areas, bore- and punch holes. A record file shows the used calculation method, no. of bends, bend informations, spring back values and the maximum dimensions of the flat pattern.
COPRA MetalBender Solver also provides extra tools to check the flat pattern and apply any necessary modification iautomatically.
For the manufacturing of the sheet metal part data exchange files for the NC-programming are created. Respective interfaces are also provided for machine control programs.
Functionality of COPRA MetalBender Solver
- Calculation of neutral line according to DIN
- Material properties
- Maschine dependent correction factors
- Use company specific know how
- Calculation of overbend angle and -radii
- Bothsided flat pattern calculation
- Take break-through objects into account
- Optimize points of intersection curves
- User defined punching tools
- No training cost