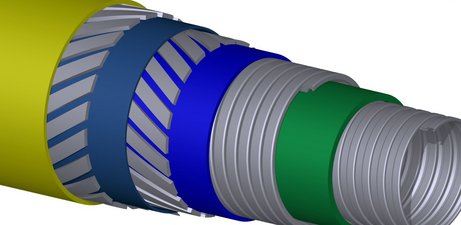
Flexible tubes for deep-sea exploitation
Optimizing the Construction of Flexible Pipes for Deep-Sea Oil andGas Exploitation
Exploiting deep-sea oil and gas resources is a major challenge for exploration and conveyance. Ideal for the purpose are flexible, multilayer pipes that are able to withstand the enormous pressure at depths of more than 1000 meters, that are resistant to corrosion and also reusable.
Particular importance attaches in construction to the design of specially profiled reinforcement of different metal materials. For the complex design and simulation processes a professional basis is presented by COPRA RF Software for rollforming developed by data M Sheet Metal Solutions GmbH. They optimize construction of the wire and sheet metal profiles, of the necessary roll forming tools, plus the winding process of metal profiles to form a stable pipe carcass. With its broad-based functionality the software very much reduces the time consumed by the design process, and high-performance simulation eliminates to a large degree the risk of design errors.
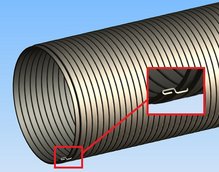
Specialized Software Simplifies the Design Process for Flexible Carcass of Wound Profiles
The inner layer of the pipe consists of metal reinforcing profiles that are wound around the longitudinal axis of the pipe and form-fitted with one another by their profile. Producing the carcass means a dual stress for the material because the sheet metal is first roll formed and then wound. A frequent problem in the winding process is the appearance of waviness on the profile edges.
If the profile at the outset of the winding process is not within certain tolerances, the stability and flexibility of the carcass can no longer be assured. The consequences of the carcass breaking could be dramatic to say the least.
Continuous Process Chain Allows Timely Fault Detection
For complex design processes of this kind data M offers tried and tested, thoroughly engineered solutions: COPRA RF for design of the profile and tooling, and COPRA FEA RF to simulate the roll forming operation and the winding process.
COPRA FEA RF simulation imports the previously generated profile and tool data and calculates deformations appearing in the profile. Because simulation of the carcass winding process can include all information found about material deformation in the first step — roll forming the sheet metal — a positive simulation result will mean that problems in subsequent practical implementation are most probably eliminated.
A FEA simulation allows different kinds of investigation direct onscreen, in other words without prototyping and machine set ups. So the designer has a simple means of finding out more about the influence of different materials, or of determining the minimum radius for a planned winding process. In each simulation they gather new, specific knowledge that is a valuable support in future projects.
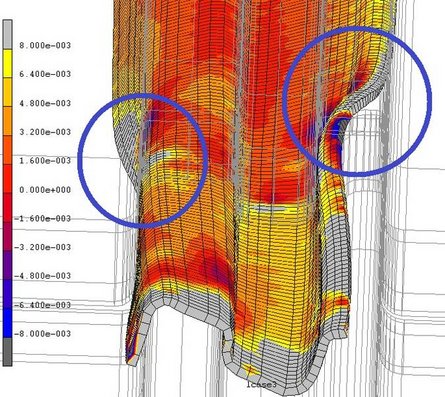
COPRA RF Wire Rolling Supports Solid Metal Roll Forming
Another challenge in the construction of flexible conveying pipes is presented by the pressure armor. This is also produced by means of a winding process from a Z-shaped profile. The starting material for this profile is solid round steel, which first has to be roll formed to create the Z-shape.
Processing material up to 32 mm in diameter, roll forming it into a Z-profile, calls for high-performance tools or machines — and an experienced designer. COPRA RF Wire Rolling software is a highly efficient means of support, for instance by automatically configuring individual roll forming stations based on the starting and end cross-section of the desired profile. What also optimizes the process is the interactive configuration of the roll forming stations based on empirical values: The designer draws the planned roll forming stations, and then the contours for all necessary roll forming tools can be derived automatically or generated interactively.
An essential element of roll forming solutions from data M is simple and speedy verification of the generated tool rolls by COPRA FEA RF Wire Rolling. The software is powerful enough to analyze the entire process in 20 to 30 minutes, so the results of any modifications are available within a very short time.